TPM賽車式維修模式在批量產(chǎn)品檢修應用
來源/作者: TPM咨詢服務中心 丨 發(fā)布時間:2017-12-06 丨 瀏覽次數(shù):
本文對中車株洲電機有限公司動車電機檢修生產(chǎn)線進行了詳細介紹,主要包括該生產(chǎn)線的運行方式、布局特征、管理技術措施等,說明其符合賽車式維修模式的特征,從而提煉出賽車式維修模式可以有效應用于類似的批量產(chǎn)品檢修應用。
關鍵詞:賽車式維修批量產(chǎn)品應用
1、TPM設備管理咨詢公司提出簡介
賽車式維修,又稱PITSTOP,這種維修模式的理念來源于方程式賽車的檢修現(xiàn)場。方程式賽車是一類高速競技比賽活動,其成敗往往取決于0.01秒的差距。在比賽的過程中,我們可以看到,當賽車進入檢修場地,只見維修人員蜂擁到車前,迅速而有序地加油、拆解、更換、安裝、調(diào)試,在短短十幾秒的時間完成一系列的動作,讓賽車重新回到賽道。通過細致地研究分析,我們可以發(fā)現(xiàn)在賽車檢修前經(jīng)過了精心的準備和周密的設計,才能在實施階段以最高的效率、最優(yōu)的質(zhì)量完成維修任務。
賽車式維修模式有幾個主要的特征:良好的團隊合作、明確的任務和責任定義、暢通和準確的溝通、精湛的狀態(tài)監(jiān)測技術應用、持續(xù)改善、不斷的技術設計與優(yōu)化、建立基準和不斷對標、培訓與實踐。賽車式維修管理的主要目標在于縮短維修時間和控制維修成本。一個良好的賽車式維修過程,是一個不斷優(yōu)化進步的過程。具體就是從后勤準備到組織計劃,到操作執(zhí)行,最后到評價反饋,多次循環(huán),從而形成一套相對優(yōu)秀的維修模式。
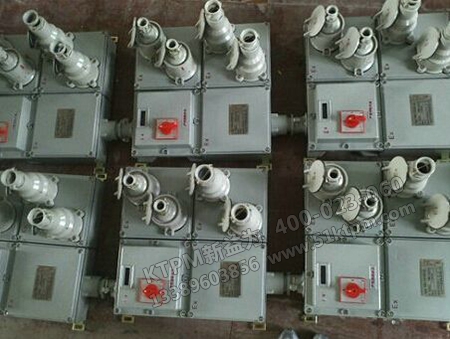
產(chǎn)品檢修應用
中車株洲電機有限公司動車電機檢修生產(chǎn)線自2012年開始引入TPM管理,經(jīng)過多年的優(yōu)化和發(fā)展,各個方面不斷完善,最終形成了一套相對高效、優(yōu)質(zhì)的檢修模式。經(jīng)過系統(tǒng)地總結(jié)分析,我們發(fā)現(xiàn)該生產(chǎn)線的檢修模式與賽車式維修模式不謀而合,并完全符合賽車式維修模式的各項特征。
2、動車電機產(chǎn)品檢修應用生產(chǎn)線介紹
中車株洲電機有限公司動車電機檢修生產(chǎn)線主要承擔高速動車組各類型牽引電機的檢修業(yè)務。由于產(chǎn)品需求的特殊性,要求該生產(chǎn)線必須在一定的生產(chǎn)周期內(nèi),完成批量的檢修任務。目前,該生產(chǎn)線有員工13人,工區(qū)作業(yè)面積550m2。根據(jù)工位制節(jié)拍化檢修模式,生產(chǎn)線被劃分為15個標準工位,檢修節(jié)拍時間為15分鐘。多年來,該生產(chǎn)線以5S、TPM、標準作業(yè)、精益改善等多項管理工具為基礎,針對人、機、料、法、環(huán)等要素不斷優(yōu)化,通過PDCA過程的多次循環(huán),實現(xiàn)了檢修效率的不斷提升和產(chǎn)品檢修成本的不斷降低。該生產(chǎn)線的班組曾多次被公司評為先進班組、TPM推進優(yōu)勝班組,并于2014年度全國TnPM大會上榮獲TnPM卓越班組獎。
2.1、各檢修要素的優(yōu)化
2.1.1、人員的合理分工和多技能培訓。
首先將生產(chǎn)線合理劃分為工序工位作業(yè),按照各工序工位對各作業(yè)人員進行專業(yè)分工,確立各工序工位作業(yè)人員的資質(zhì)要點,然后組織開展相關崗位培訓,最后通過理論與實作考核來評定,對于特殊崗位作業(yè)人員進行指明作業(yè),針對各工序工位編制作業(yè)人員信息卡,加強作業(yè)人員資質(zhì)管控。同時對于熟練操作的崗位工人,通過采用多能工的技能培訓方式,提升該崗位人員的多方面技能,從而打造多星級員工。
2.1.2、設備的有效管理和TPM活動開展。
生產(chǎn)線的設備、工裝等分布合理,借助人機工程學將設備與生產(chǎn)線布局緊密結(jié)合起來,綜合考慮設備使用頻次與人員操作便利性等,保障設備最大使用率。持續(xù)有效地開展TPM活動,采用自主改善、OPL一點課、TPM小團隊活動等形式,充分調(diào)動全員自主參與的積極性,使員工對生產(chǎn)過程中所要用到的設備、工裝、工具等硬件設施,除做到日常的維護保養(yǎng)外,還充分掌握其使用狀態(tài)、熟悉其使用性能,并且主動提出改善項點,能夠進行較為簡單的故障維修。通過全員自主參與的生產(chǎn)維護活動,使設備性能達到最優(yōu),提高設備綜合效率。
2.1.3、備件的標準化管理。
對生產(chǎn)線所用的備件進行全面系統(tǒng)的梳理,制定各工位物料詳細清單并目視化,同時針對各工位物料設計專門的物料配送工裝,按照單臺或多臺的標準進行配置物料,在配送工裝上對于不同類別的物料做形跡區(qū)分和色標管理,有效防止了物料混裝、配送出錯等問題,實現(xiàn)了物料從庫房、配送到使用的標準化管理。
2.1.4、工藝布局的不斷優(yōu)化、拉動式節(jié)拍化生產(chǎn)和標準作業(yè)。
首先對現(xiàn)場工藝布局進行優(yōu)化,運用單件流作業(yè)方式對現(xiàn)場工藝布局進行調(diào)整,將前后各工序有機的聯(lián)系在一起,采用U型布局結(jié)構(gòu),設計兩條并行作業(yè)流水線,將生產(chǎn)線整體拆分為兩大支線,同時將兩條生產(chǎn)支線通過軌道有效連接起來,然后匯總進行組裝為成品,實行了拉動式生產(chǎn)。在兩條作業(yè)流水線上將各工序按照先后檢修工藝次序進行合理組合,利用U型結(jié)構(gòu)設計設備布局,結(jié)合多能工操作,體現(xiàn)出一人多能的作業(yè)布局特點。在生產(chǎn)過程中采用看板管理拉動節(jié)拍化模式,運用生產(chǎn)實績表對各工序工位作業(yè)時間進行統(tǒng)計,分析各工位作業(yè)均衡率,對瓶頸工位進行持續(xù)優(yōu)化,平衡各工位作業(yè)時間,提升均衡化檢修水平。結(jié)合生產(chǎn)節(jié)拍進行分析,找出關鍵影響因素,持續(xù)對作業(yè)方法進行改進與優(yōu)化,提高作業(yè)效率,保障節(jié)拍化生產(chǎn)。同時實時統(tǒng)計現(xiàn)場生產(chǎn)異常信息,并定期對異常情況進行分析,組織各部門相關人員進行研討,圍繞異常問題制定相應的改進措施,保障生產(chǎn)正常進行。為提升作業(yè)過程中的質(zhì)量管控,針對現(xiàn)場推進標準作業(yè)并持續(xù)優(yōu)化,組織完善標準作業(yè)組合三票(標準作業(yè)指導書、標準作業(yè)卡片和標準作業(yè)組合卡),將現(xiàn)場作業(yè)標準化、規(guī)范化,指導員工進行操作。
2.1.5、安全、舒適、規(guī)范的現(xiàn)場環(huán)境。
生產(chǎn)線采用環(huán)氧薄涂地面,現(xiàn)場明亮整潔、標識明顯,空調(diào)、風扇等相關設施配套齊全。針對各工序工位制定現(xiàn)場安全定置圖與防范要點,提升員工安全作業(yè)環(huán)境認識水平,規(guī)范現(xiàn)場安全操作行為,讓員工掌握現(xiàn)場各工序工位作業(yè)安全環(huán)境要領,能夠有效識別現(xiàn)場存在的安全隱患并做出預防措施。針對員工提出的需求,不斷地優(yōu)化現(xiàn)場作業(yè)環(huán)境,使員工保持愉快的工作心情。
2.2、PDCA過程的執(zhí)行
2.2.1、后勤準備。
在批量產(chǎn)品檢修前,組織各部門提前做好準備工作,主要從設備、制造、采購、售后等方面進行前期準備。對于定期檢修產(chǎn)品,前期將組織相關部門對產(chǎn)品運行情況進行跟蹤,定期反饋運行信息,然后針對運行的情況進行分析,預估產(chǎn)品檢修的周期,同時結(jié)合之前配件檢修更換的數(shù)據(jù)信息預判各部件的故障率,提前做好備品備件的預投產(chǎn)。同時做好模擬生產(chǎn)流水線與配送線的建設,提前發(fā)現(xiàn)可能存在的問題。針對現(xiàn)場設備每天進行點檢、定期校檢,并做好定保修,針對設備關鍵部件提前備料,對于工模量刃每天做好開工前確認,同時做好設備與工模量刃日常保養(yǎng)與維護,提前發(fā)現(xiàn)有存在的故障隱患及時排除。
2.2.2、組織計劃。
為了保證計劃合理執(zhí)行,主要從有效的生產(chǎn)管理、異常突發(fā)問題處理以及工具工裝優(yōu)化等方面進行提升。針對產(chǎn)品檢修存在不均衡的特點,為了更有效的組織產(chǎn)品檢修作業(yè),制定周計劃、三日計劃及日滾動計劃。制定車間、班組、工位三位一體異常管控措施,構(gòu)建異常信息處理網(wǎng)絡,做好異常問題快速響應機制。同時設計儲運轉(zhuǎn)運一體化工具工裝,減少中間二次轉(zhuǎn)運。搭建標準化作業(yè)工作臺位,以最優(yōu)操作的原則為中心,推進工模量刃三定管理,減少工模量刃在使用過程中的出錯率。
2.2.3、操作執(zhí)行。
為落實操作執(zhí)行力,強化了質(zhì)量三檢制管控、人員及分工管理和工作績效評估等方面。首先為達到穩(wěn)定的工作狀態(tài),對員工進行標準化作業(yè)管理,將各工序工位主要作業(yè)內(nèi)容進行固化,形成標準化作業(yè)模式;同時定期推進員工輪崗作業(yè),提高員工多技能水平,盡可能的減少人員波動影響。對于工作計劃定期進行檢查,并將員工工作完成情況納入到績效管理中來,通過工作量完成情況、員工日常表現(xiàn)等多方面來評定員工績效,督促員工在工作中更好的保質(zhì)保量完成檢修任務。在檢驗過程中,嚴格按照質(zhì)量三檢制原則(即自檢、互檢、專檢)對產(chǎn)品及備件進行檢查,確保產(chǎn)品及備件質(zhì)量合格。
2.2.4、評價反饋。
通過持續(xù)總結(jié)分析,提煉好的檢修方法與經(jīng)驗,并逐步進行規(guī)范,形成統(tǒng)一的標準。經(jīng)過一段時間的運行,定期對產(chǎn)品檢修工藝質(zhì)量設備等方面進行總結(jié)分析,持續(xù)推進改善,將復雜事情簡單化、簡單事情標準化、標準事情常態(tài)化。通過持續(xù)不斷的改進與優(yōu)化,將產(chǎn)品檢修進行標準化設計,融合現(xiàn)場人、機、料、法、環(huán)五要素,從制度管理、廠房布局、生產(chǎn)管控、作業(yè)管理、目視管理、品質(zhì)管理及改善等七個模塊進行細化,以服務現(xiàn)場為中心,將各模塊管理內(nèi)容不斷進行優(yōu)化,并逐步向外進行延伸拓展,然后形成標準化管理。
2.3、相比于PITSTOP的亮點
2.3.1、工位作業(yè)后員工自檢,及時發(fā)現(xiàn)作業(yè)質(zhì)量問題。
動車電機檢修生產(chǎn)線在產(chǎn)品交驗的終端,配備了專職質(zhì)檢員進行質(zhì)量檢查。同時,針對每個工位,要求生產(chǎn)員工在作業(yè)完成后對自身的作業(yè)質(zhì)量進行自檢,按照自檢卡片的要求填寫相關作業(yè)參數(shù),并填寫自檢記錄。通過員工的即時自檢,可以讓員工發(fā)現(xiàn)自身作業(yè)過程中的錯誤和不足,及時糾正和改善,從而加強了產(chǎn)品的質(zhì)量檢驗,更好的避免產(chǎn)品質(zhì)量問題的發(fā)生,提升產(chǎn)品質(zhì)量。
2.3.2、相對平衡的工位作業(yè)時間,充分實現(xiàn)均衡化檢修。
定期組織各部門人員對現(xiàn)場檢修生產(chǎn)線運行情況進行評估,對各工序工位作業(yè)實際時間與節(jié)拍時間進行對比分析,找出差距,然后從作業(yè)方法、人員操作合理性等方面進行持續(xù)改進。同時針對各工序工位之間進行平衡分析,將作業(yè)時間較長的工序工位作業(yè)做為瓶頸工序,建立專門的改善團隊來解決瓶頸問題,從而盡量保持各工序工位作業(yè)時間的均衡性,減少各工序工位之間的等待浪費,使生產(chǎn)過程中人員、設備等使用率達到最大化,實現(xiàn)均衡化檢修。
3、結(jié)語
2016年5月,針對動車電機檢修生產(chǎn)線開展TPM示范線建設項目,項目的主要目標在于打造標桿培訓道場、提升生產(chǎn)線多能工率和建立完善的人員成長體系。目前項目的各項工作開展順利,通過TPM示范線的建設,動車電機檢修生產(chǎn)線的PITSTOP模式必將走上更高的臺階。賽車式維修是在極短的時間內(nèi)獲得超高的完好性水平的維修方式。賽車式維修模式在動車電機檢修生產(chǎn)線的成功應用,絕對不是偶然。相信通過深入分析賽車式維修模式的思想和理念,成功地轉(zhuǎn)化和付諸實踐,其必定能夠廣泛應用于類似的批量產(chǎn)品檢修應用,實現(xiàn)批量產(chǎn)品檢修水平的有效提升。
- 上一篇:TPM用觀察法診斷數(shù)控機床故障
- 下一篇:TPM設備維修費用管理