一個有問題的人是活人,一個有問題的企業(yè)是正處于成長中的企業(yè),而一臺出現(xiàn)了問題的設備則證明設備還有改進的空間。不管是大型重工設備,中型數(shù)控設備,還是小型手工操作設備,按照4M1E人、機、物、法、環(huán)的管理模式進行分析后我不難發(fā)現(xiàn),設備管理是企業(yè)設備效率分析乃至生產(chǎn)管理的一個重頭戲。因為設備是整個生產(chǎn)流程的主體資本。而OEE是設備效率提升的一種有效管理模式。
如何利用設備資源,使其成為公司價值創(chuàng)造的 “整容師”。而固有的設備水平式垂直布置及落地生根,在現(xiàn)實的生產(chǎn)中已被拋棄與淘汰。提高設備可動率及快速換線、全員設備效率提升已經(jīng)成為新的設備改善起點,同時也將載入新生產(chǎn)技術(shù)歷史的一頁。
鑒于從事設備管理工作,在很大程度上我對設備的全面改善及設備效率提升負有很大的責任,本著對公司對崗位負責的態(tài)度,在公司領(lǐng)導的重視與推薦下,我有幸參加了全國高科技教工委的設備效率OEE培訓管理課程,讓我認識到了每一個生產(chǎn)設備都有自己的最大理論產(chǎn)能,要實現(xiàn)這一產(chǎn)能必須保證沒有任何干擾和質(zhì)量損耗。
設備效率分析
當然,實際生產(chǎn)中是不可能達到這一要求,由于許許多多的因素,車間設備存在著大量的失效: 例如除過設備的故障,調(diào)整以及設備的完全更換之外,當設備的表現(xiàn)非常低時,可能會影響生產(chǎn)率,產(chǎn)生次品,返工等。
除此之外,更重要的是讓我近一步認識到了設備效率的重要性與具體改進方法,因為設備綜合效率的提高,是生產(chǎn)率水平的提高,也就是以少量的輸入產(chǎn)生良好的輸出效果。 具體表現(xiàn)為:
產(chǎn)量(P-Production):需要完成的生產(chǎn)任務,即設備的生產(chǎn)效率要高。
質(zhì)量(Q-Quality):能保證生產(chǎn)高質(zhì)量的產(chǎn)品,即設備有利于提高產(chǎn)品質(zhì)量。
成本(C-Cost):產(chǎn)品成本要低,即設備能源、原材料等耗費少。
交貨期(D-Delivery):設備故障少,不耽誤合同規(guī)定的交貨期。
安全(S-Safety):設備的安全性能好,設備對環(huán)境污染小,文明生產(chǎn)。
士氣、勞動情緒(M—Morale):人機匹配關(guān)系較好,使作業(yè)人員保持旺盛的
工作情緒。
通過本次課程的學習,我不但了解到諸如日本、韓國等著名企業(yè)的設備效率提升方式外,還吸取到了國內(nèi)部分企業(yè)諸如賽格-三星公司、上海寶鋼集團、廣東科龍集團、濟南將軍集團以及正在推行設備效率改善與管理的青島海爾集團等大中型制造型企業(yè)的成功效率改善模式。再回頭分析我們公司的設備管理狀況,有諸多好的方面,也有好多不利因素一直困擾設備正常效率以及設備效率最大化的發(fā)揮,其中之一就是我們對設備六大損失分析不夠透徹,即停機損失、換裝調(diào)試損失、暫停機損失、減速損失、啟動過程次品損失以及生產(chǎn)正常運行時產(chǎn)生的次品損失。
再者就是我們對設備的效率OEE分析過于客觀判斷,這也是在本次學習中對我影響最為深刻的地方,因為設備損失與設備效率分析直接影響到我們企業(yè)的命脈。例如: 一次性打火機生產(chǎn)線的速度是一秒鐘一個(3600個/h),小汽車生產(chǎn)線的裝配速度為45~60S一臺(60~80臺/h)。如果一臺機器出了故障,一個小小的螺釘不能及時到位,一小時就有3600個打火機,60~80臺小汽車在生產(chǎn)線上進退不得。如果一個小小的螺釘質(zhì)量有問題,一小時就有3600個打火機,60~80臺小汽車存在質(zhì)量隱患,不一定哪天會給顧客帶來麻煩。
如果沒有訂單就投入生產(chǎn),下道工序還沒有需求,上道工序已加工完成,意味著每小時就產(chǎn)生3600個打火機的中間產(chǎn)品庫存,60~80輛小汽車中間產(chǎn)品的庫存。庫存需要的建筑物、包裝、搬運費用,原材料流動資金占有費用浪費,以及中間環(huán)節(jié)造成中間產(chǎn)品的損壞費用是大大的浪費。這對公司來說是一個致命的沖擊。所以我也極力地將這種設備效率OEE分析與管理模式應用到我們的企業(yè)實際管理當中,以求從成本與效率的角度著手改善,使設備效率最大化發(fā)揮,從設備可動率與稼動率層面尋求分析改進空間。
課程中的聆聽與實際中的對接,在正確的設備管理思維中讓我得到了最大的啟發(fā),原來我們一些錯誤的設備效率分析與保養(yǎng)觀念已經(jīng)不再能為企業(yè)及生產(chǎn)現(xiàn)場帶來顯見的效益。只有修理,沒有保全;稼動率與可動率沒有區(qū)分;只有救火的觀念,沒有防火意識;只有單兵作戰(zhàn),沒有整體規(guī)劃;作業(yè)員歸操作,維修員歸維修;以及迷信高速度、高性能的機器設備等諸多設備管理方式正在對我們的設備效率帶來巨大的損失。
也相信通過本課程的學習與應用,我應該更多的在現(xiàn)有設備時間開動率、性能開動率,以及合格率方面投入更多的精力進行改善,因為當來自時間,速度,質(zhì)量的損失被綜合在一起,最終OEE數(shù)字反映出任何設備或生產(chǎn)線的運行狀況才是現(xiàn)場最真實的設備效率展現(xiàn)。
我深刻地了解到,時間開動率、性能開動率、合格品率是由每一工作中心決定的,但每個因素的重要性,因產(chǎn)品、設備、和涉及生產(chǎn)系統(tǒng)的特征不同而異。例如,若機器故障率很高,那么時間開動率會很低;若設備的短暫停機很多,則性能開動率就會很低,只有三者數(shù)值都很大時,設備綜合效率才會提高。故此我想我們應該掘啟傳統(tǒng)的設備修理與恢復性無效工作,更多地應該從設備的更新與改造、以及從設備稼動率考慮,努力提升設備素質(zhì)與人員素質(zhì),不斷追求設備的高效率工作,這樣才能從設備效率角度為公司創(chuàng)收更大的經(jīng)濟效益,降低設備運營成本及維修費用。
但值得公司關(guān)注的是,要改變設備現(xiàn)狀,全方位設計與更新設備現(xiàn)有水準,讓設備產(chǎn)生高效能的OEE全能效率發(fā)揮,除建立建全公司體制外,還需公司內(nèi)部職能部門的配合與協(xié)調(diào)。這一點也是公司設備從原始走向效率化的必經(jīng)之路。首先應制定公司內(nèi)部設備規(guī)范化操作標準與設備更新檢驗規(guī)程,應從維修程序規(guī)范化、備件管理規(guī)范化、前期管理規(guī)范化、維修模式規(guī)范化、潤滑管理規(guī)范化、現(xiàn)場管理規(guī)范化、組織結(jié)構(gòu)規(guī)范化以及其它規(guī)范化方面著手擬定,規(guī)定相應實施周期,公司領(lǐng)導應給予全力支持并當作公司設備效率化的重中之重,并納入公司經(jīng)營計劃與設備目標管理的范疇,火車跑得快,全靠車頭帶,公司領(lǐng)導就是設備效率化改進與更新的導炎索。
其次就是需要公司職能部門的通力配合與相互支持,作為處于生產(chǎn)一線的制造與生產(chǎn)部門,應嚴格按照設備管理部門制定的標準設備操作規(guī)程進行操作及嚴遵設備保養(yǎng)周期,掌握與控制設備使用頻率,消除設備現(xiàn)場浪費,充分設備潤滑與保全管理,確保設備使用壽命,在重視產(chǎn)品效率的同時更應保證設備再生效率的保障,二者相輔相成,因為產(chǎn)品效率是凌駕于設備效率的基礎(chǔ)之上。
作為設備采購部門,雖然成本控制與縮減是采購職能的一大管理因素,但不能因為盲目地一味追求低成本而忽略設備性能率與可動率,在節(jié)省成本的誘因下改變設備使用需求本質(zhì),從而撿了玉米卻丟了桃子,由此而造成的設備低效率運作及性能低下,并牽動人工成本的增加與制造不良返工、設備使用壽命縮短等不良反應,則遠遠大于設備的初期采購成本,這也是設備采購的致使弱點。
再就是作為設備管理及工程設計部門,單一化的設備設計在很大程度上影響了設備可動率的使用頻率,造成設備的專一化與產(chǎn)品的單品化對應,從而使多數(shù)設備因過于單一化生產(chǎn)而停滯封存,再者就是設備功能性的設計缺陷,從根本上限制了OEE設備效率的全速發(fā)揮,要么失效停工,要么修復頻繁。作為現(xiàn)場設備的“兩書”并置,以及操作人員的“三會四要”,須品質(zhì)、生產(chǎn)、工程、設備等部門的極力參與,從良品率、性能開動率及時間開動率等效率化方面全面啟動公司設備OEE的導入實施。
在學習過程中,通過老師講解及與學員之間的相互溝通,我得到了一組確切的數(shù)據(jù)回饋,日本企業(yè)通過設備OEE實踐擴增了產(chǎn)能效率化的60%,而我們中國部分企業(yè)目前已經(jīng)通過設備OEE實踐提升了原有產(chǎn)能的40%,個別企業(yè)已經(jīng)達到了58%,趕上了日本企業(yè)2000年的作業(yè)水平。這也是值得我以及公司相關(guān)人員應該去探究的一個可觀性因素。而因設備OEE的充分利用與實施,其從成本的角度考量也為我們提供了一組值得深受啟發(fā)的數(shù)值參考,就美國和日本的制造業(yè)而言,設備管理及設備OEE效率化提升占銷售收入的平均百分比為53%,當設備OEE效率化提升5%時,則利潤增加270萬元。若欲獲得相同的結(jié)果,則直接人工必須降低22%,制造費用必須降低24%。因此不難看出,無論是從成本還是效率方面都是值得我們?nèi)⒃O備OEE效率化的一大基本原因,因為以上的結(jié)果就是來自他們的實踐,相信公司也可以按即定目標實施達成。
在此通過兩天的學習與討論,我總結(jié)出了公司目前實施設備全面保全及設備OEE效率化的十大問題癥狀:
1、照本宣科,死搬硬套,導致系統(tǒng)中斷;
2、沒有文件支撐,無標準的維修,導致維修超標;
3、設備故障依賴于維修人員,產(chǎn)修對立效應
4、設備責任不明確,空間與時間的浪費;
5、型號追求極端化,沒有考慮實質(zhì)分析;
6、部件存量過剩,缺乏規(guī)劃周期;
7、忽略治工具維護,帶動設備故障邊際效應;
8、誤認為保養(yǎng)就是大掃除,觀念錯誤出現(xiàn)應付;
9、設備考核指標不明確,導致重心失控;
10、設備使用專一化,人員調(diào)整頻繁,無多能工。
立足本職工作崗位,就應該充分發(fā)揮自身的工作能力,爭取學習更多的工作技能,通過OEE模型的各子項分析,準確清楚地發(fā)現(xiàn)與分析設備效率如何,在生產(chǎn)的哪個環(huán)節(jié)有多少損失,以及可以進行那些改善工作。通過使用OEE工具,可以輕松的找到影響生產(chǎn)效率的瓶頸,并進行改進和跟蹤。
TPM管理咨詢公司提出:達到提高設備效率分析的目的,同時使公司避免不必要的耗費。為此我希望通過OEE的改善,使企業(yè)的設備時間開動率不低于90%,性能開動率不低于95%,合格品率不低于99%,這樣設備綜合效率才不低于85%。這也是我通過本次課程學習后進一步對設備管理的目標設定。同時,力求通過對設備綜合效率的統(tǒng)計與分析,系統(tǒng)地找出阻礙設備綜合效率提高的因素,提出改善或糾正措施,確保企業(yè)的持續(xù)改進,實現(xiàn)企業(yè)效益最大化。
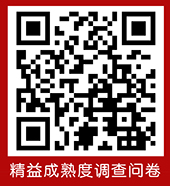